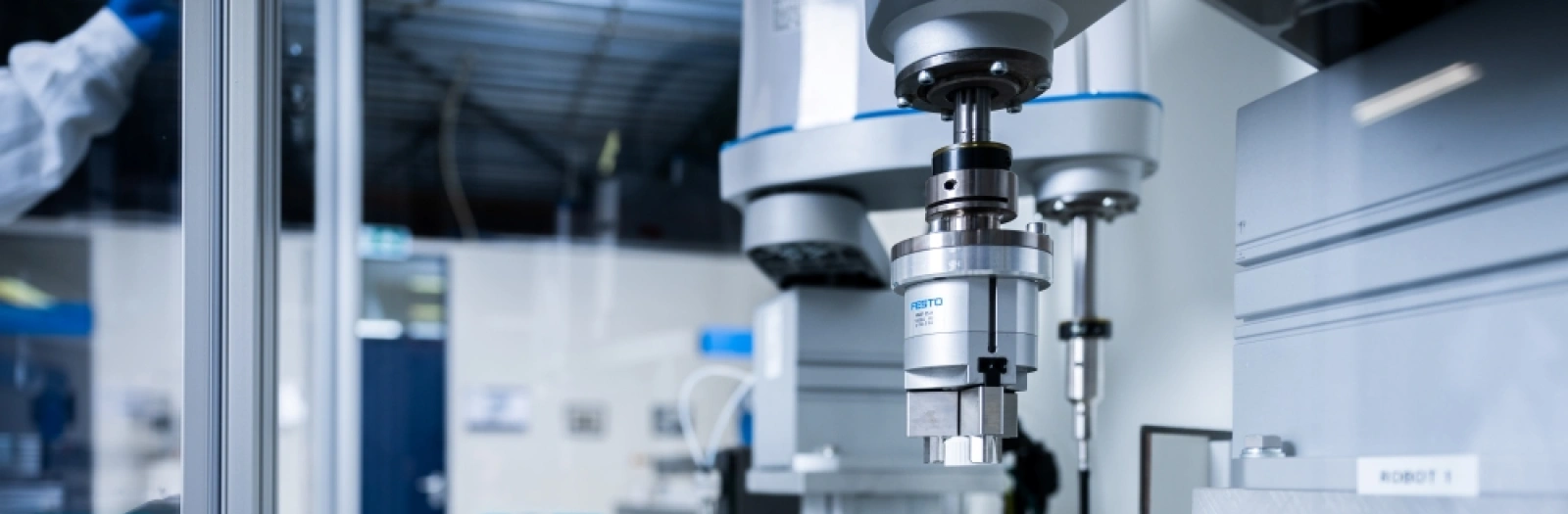
Automated Lysis Preparation Robots
Synchron has developed two new systems for application in the agro industry, focusing on automating labor-intensive process steps, resulting in two efficient systems that perform specific labor-intensive tasks. Incubation, a non-labor-intensive process step, remains manual to maintain system efficiency.
Enza Zaden, an international vegetable breeding company and third-generation family business, develops new vegetable varieties in over 31 crops, such as lettuce, bell peppers, tomatoes, cucumbers, radishes, and onions, with worldwide seed production and sales.
Within the seed health department, ENZA tests vegetable seeds for viruses, viroids, bacteria, and fungi, often using 50 ml centrifuge tubes. Repetitive tube opening and closing are seen as cumbersome, prompting ENZA to seek automation solutions.
Our TTS Solution for automated Lysis Preparation
How it was addressed:
Synchron evaluated available "proven technology" for process steps and adapted existing building blocks for decapping, tube handling, and pipetting to meet customer and application requirements.
Disposable tips:
A fast method using the same arm for decapping was adopted, ensuring compatibility with tube caps.
Customer benefits:
ENZA now has two fully automated systems that handle labor-intensive process steps, improving speed (tubes/minute) and accuracy, allowing employees to focus on other tasks.
Quantification:
Market/Industry/Module: Agbio – SeedHealth
The Process/workflow
System 1 (Tube Filling):
1. Operator loads the machine with tubes and liquid.
2. Operator sets the desired dispense quantity and starts the machine.
3. Robot process:
a. Robot picks up a tube and moves it to the decapper.
b. Cap is removed from the tube, robot holds the cap and makes way for the dispense arm.
c. Dispense arm adds the desired amount of buffer.
d. Robot screws cap back onto the tube.
e. Tube is placed back in the rack, and the next tube is picked up.
4. Operator unloads the machine.
System 2 (Tube2Plate):
1. Operator loads the machine with tubes and liquid.
2. Operator sets the correct crop and system parameters and starts the machine.
3. Robot process:
a. Handling robot picks up a tube and moves it to the decapper.
b. Cap is removed from the tube, handling robot holds the cap and makes way for the pipetting robot.
c. The pipetting robot picks up a disposable tip and extracts the desired sample volume from the tube, taking precautions to prevent contamination.
d. The pipetting robot transfers the sample to the deep well plate.
e. Handling robot screws cap back onto tube.
f. Tube is placed back in the rack, and the next tube is picked up.
4. Operator unloads the machine.
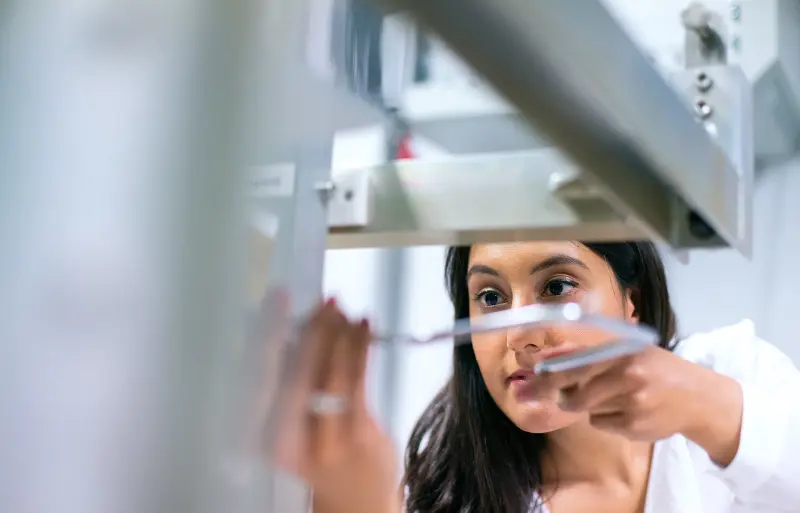
IF WE CAN THINK IT, WE CAN BUILD IT
Discover Your Possibilities
Discover the next level of laboratory workflow automation and elevate your sample handling processes to new heights. Reach out to us today and embark on the journey of revolutionizing your research with cutting-edge automation solutions.
Key Features
Industrial robotic arms
Disposable pipetting adapter
Gripper fingers for transportation of 50 ml tubes
Syringe pump for pipetting deepwell plate
Tube racks holding 32 tubes
Waste station for disposable tips
Flush station
Gognex Camera
Touch panel
Why Automate?
-
Labor-intensive (RSI)
-
Safety (harmful lysis buffer)
-
Speed Advantages